
There’s an old expression in both the Project Management and Quality Improvement businesses: “There are three criteria that go into deliverables—good, fast and cheap. Pick any two.” Sometimes called the “Iron Triangle,” it has both literal and figurative application to reloading your own ammunition as well.
While cases and bullets, powders and primers are the essential components of every assembly method, and the steps therein the same, choosing the fabrication hardware has crucial implications for how the Iron Triangle tilts in your favor. Note our use of the word “tilt”: Get comfortable with the idea that there’s still no way to beat it.
If we start with “good” and “cheap,” there’s a method that is both time-honored and difficult to fault across a positively huge range of calibers—single stage. As “single” likely implies, one operation at a time is occurring as cartridges come together from components, and as you may recall, seven core steps are required. Granted, some of the two-for-ones still apply, as work gets done on both the up and down stroke of the “press.” This corresponds to one up/down cycle of a handle, and powers a “ram” mechanism that moves the case up and down into dies. Sizing/de-capping, re-priming/flaring, charging, bullet seating and crimping proceed in batches of lotted of cases, usually grouped by length and/or headstamp. (Lotting reduces the amount of die adjustment for flaring, seating and crimping steps.)
“Good” manifests itself mainly as high precision in the single-stage world. Still, an awful lot of serious shooters build their ammo this way—especially for rifle. The “cheap” part of the formula is readily apparent in the acquisition of the base hardware. This space has long lodged an 800-pound gorilla by RCBS named the “Rock Chucker,” with the entire kit running a smidge over $300. Add a dial caliper for measurements, consumables (cases, bullets, powder and primers), and dies for your caliber, and you can be making rifle or pistol ammunition in short order. Simple in setup and maintenance, it’s also a great way to understand the ins and outs of fabrication and safety without overlaying too much in terms of hardware complexity. The “feel” is also unrivaled: Because only one operation is occurring in a given part of the press stroke, you’ll quickly develop a sense for when things are going well or poorly, and this in turn translates into high cartridge quality and good process safety.
“Fast” isn’t really in the cards for single-stage reloading. It doesn’t take much imagination to see that each case must be handled multiple times before a completed round emerges. Still, an orderly setup and practiced hand can produce more than 100 rounds per hour of truly excellent ammunition.
The next step—at least in speed—is the so-called turret press. In a turret rig, you don’t have to replace one die with another to gain access to the ram. Instead, a rotating head—the turret—allows the needed die to be spun into position over the ram, and the required operation performed. Turret presses can have as few as two die positions (the fine Harrell Precision boasts two, three or four at the customer’s option, here) and as many as seven (Redding T-7), and heads are removable. This means you can dedicate a head to a given caliber, and dramatically reduce the amount of adjustments or other tinkering needed in caliber swaps.
The Redding T-7 is likely the bully on this particular playground, and deservedly so. Battleship-class construction goes hand in hand with smooth, precise operation, and stakes out an enviable middle ground in terms of speed vs. quality: You can pretty easily double the output of a single stage setup. Quality losses? Tiny, if at all. … this in turn translates into high cartridge quality and good process safety.
Turret presses are generally underappreciated in our view, and are particularly well-suited to reloaders who want to fine-tune—or perhaps ultra fine-tune—their cartridge parameters. This benefit is two-phased, if you will: First, short runs are a piece of cake in turret rigs because die-swapping (a la single stage) is unnecessary, and there are no unnecessary operations or incomplete rounds as in progressive machines (we get to these next).
Second, the open nature of turret systems is tough to beat. There always seems to be plenty of room to work, either on the cartridges themselves, or to make the adjustments needed to various dies, pins or plugs. In many circumstances, you can leave an entire turret position unoccupied next to oft-adjusted tools. It keeps the mumbled—or perhaps not so mumbled—cursing to a minimum.
These connive at our posited benefit. If you just need 10 of “those” to chrono, or 20 of “that” for action-proving (a new bullet shape, say), you’ll never want to do them on another system once you’ve done them on a turret. Particularly if you invest in additional heads, even jumping between small batches in different calibers is a piece of cake. And for the “staging” of cases, generally meaning sized/primed/flared? Turrets wax everything else for this prepper (capital or lower case “p,” your choice) specialty: You can charge, seat and crimp with lightning speed somewhere down the line when needs for a particular shooting task becomes clear.
Precise experimentation is uncommonly straightforward then, perhaps even tempting. We wouldn’t be a bit surprised to discover that turret guys (and gals) get to the best ammo earliest and easiest in their reloading “lives” due to this all-but-painless flexibility.
Turret systems can also grow slowly–you don’t have to have extra heads to load new calibers, but you can add them over time as need and budget allow. Figure a turret system will run about $550 to get running (though a T7, by itself is a paltry $300 or so), as you still need things like a powder measure, scale and caliper.
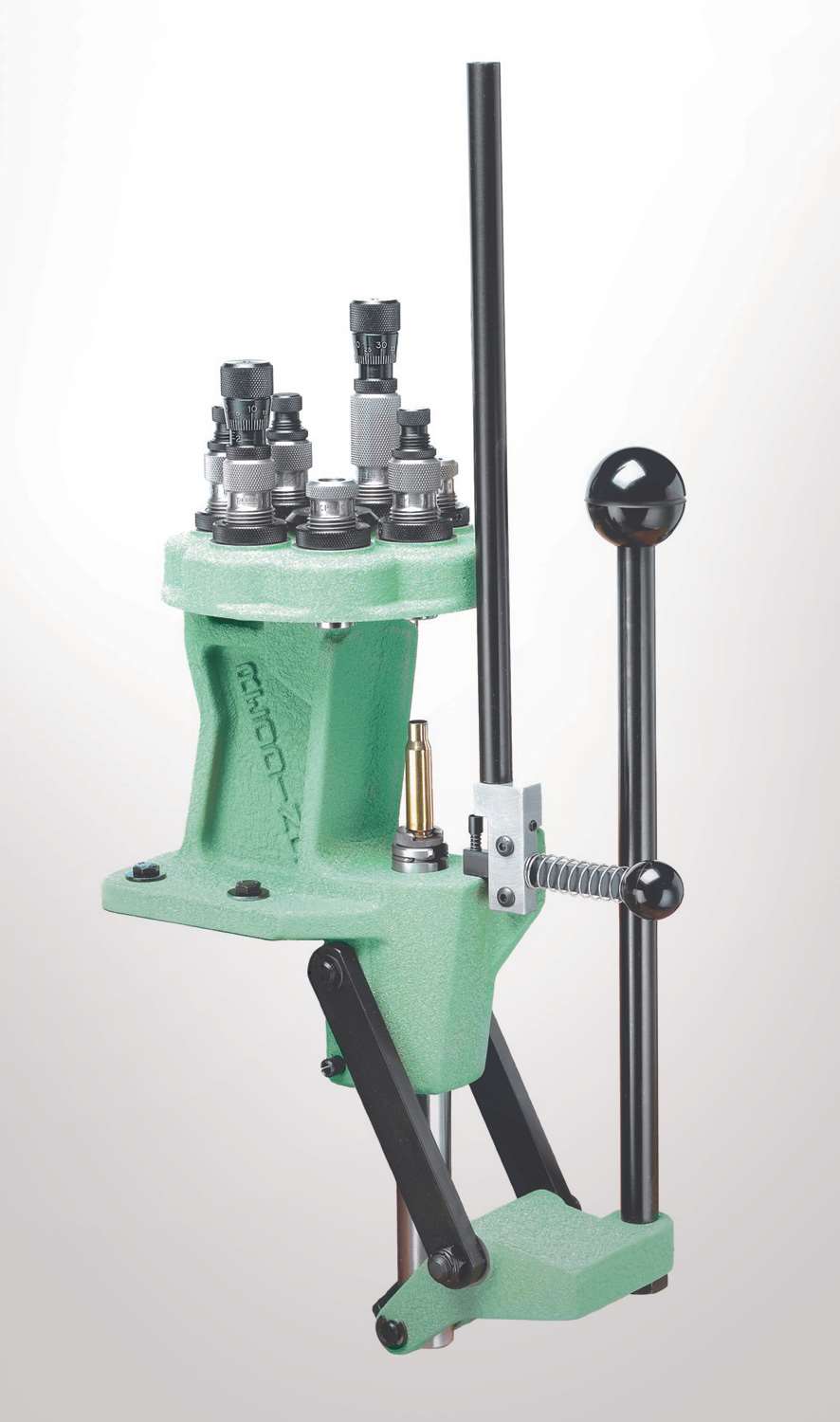
Last but in no way least are the so-called progressive reloading systems. Most folks rightly consider these the big dogs, and they can be undeniable powerhouses in terms of turning modest investments of shop time into range time (read “spent brass”). You’ll search high and low for a “B” shooter or higher in almost any competitive venue who isn’t using one.
The heart of these systems is essentially a turret in reverse. Loaded one at a time, cases ride a rotary shell plate and “progress” through a prep or assembly step as they are raised into stationary dies or lowered onto tools, for primer seating, say. Once each station is filled, a completed cartridge emerges with every subsequent pull of the handle/cycle of the ram. 300 rounds per hour is cake with simpler, less expensive machines, and 1,000 or more is possible at the top end.
You read that correctly: An arm-powered progressive press can turn out 1,000 rounds an hour.
Some machines use as few as four positions to do our seven tasks, while others add more positions for jobs like primer pocket uniforming (technically, “swaging”). Are more positions better? Well, yes—but as we said in Part 3, these are refinements. But they do inarguably speed things up, generally by simplifying or eliminating pre-build tasks.
A crucial differentiator here is called “indexing.” There are two flavors—manual and automatic—and the nomenclature indicates whether ram/handle movement advances the progressive turntable via some sort of cam or other transmission, or whether you push it by direct action. We’re hesitant to call one inherently superior to the other, except that auto machines, running perfectly, are nearly always faster. But what is most inclined to foul up an auto machine? Misindexing. If it goes wrong enough, press components can be damaged or broken, and this can slow you down in a huge—and protracted—hurry. Put it this way: We know what can bend/break/fail on ours, and try to have two replacements on hand at the minimum.An arm-powered progressive press can turn out 1,000 rounds an hour.
Manual indexing is mechanically far simpler, and in this sense much more reliable. The trouble here is speed, and remembering to do it. If you get distracted and double-charge a case, nothing good happens next. If you catch it, it’s usually because of a charging overflow. A mess, it’s true, and one that must be meticulously amended (those little flakes of powder always get where they don’t belong), but eminently fixable.
If, however, you’re loading a smallish charge of an “unfluffy” powder in a largish case, you may find yourself in worse trouble, albeit down the road. You can blithely continue assembly, with a double charge looking for all the world like a safe cartridge. Right up until you blow up your gun, or at least seriously damage some components (like magazines) and your confidence. (Though common, it’s a bad practice to think you can find these by weighing finished cartridges. Charge weights are measured in grains, or 1/7000 of a pound. If you’re stoking up a largish case, a double might reach a threshold where they’d be detectable, but the variation of cases, bullets and scale can easily be more that the 3.5 to 5.0 grains you’re looking for.)
Any reason we need explain why powder-sensing systems are common, popular accessories in the progressive press world? Thought not …
In any event, progressive presses are still “the bomb” in many respects: With loaded primer feed tubes, we’ve run 600-plus rounds an hour through our positively ancient rig. We keep this in service as much because we’re used to it and have a good store of spares, but buying almost anything today would be superior: Dillon Precision has four good choices ranging from about $450 to $1,900 (we completely, utterly covet the legendary Super 1050). But Hornady’s Lock-N-Load AP is a gem too—and arguably the most “growable” (a starting MSRP of $549). It’s expandable to commercial-type rates of 800-plus rounds per hour. It also harkens a bit to the roominess we applauded in the turret systems.
Perhaps obviously, the progressive presses tilt the Iron Triangle toward “fast” and “good.” Cheap—and by that we mean acquisition cost—is a little tougher to come by. But as proof, we’d offer our recent adventure to USPSA Optics Nationals: 800 “match” rounds took less than two hours to build, made power factor easily and precisely (less than 2 percent variation despite a nearly 5,000-foot elevation and 25-degree temperature change), and had a failure rate of zero. The savings were just shy of 50 percent over what purchased “match” fodder would have cost.You won’t increase output by just slamming the lever up and down faster, but you will break stuff.
A last note on progressive presses. Most folks can make them work fine with a little patience, but don’t expect it to be an afternoon’s work. The top outputs, however, take more practice and knowledge to reach, and the barrier is almost always the same: You won’t increase output by just slamming the lever up and down faster, but you will break stuff. We’ve some experience with just about everything out there, and the crucial takeaway is to be smooth. What makes this tricky is that “smooth” is a different commodity on each type of press. Camming points for shell plate rotation or priming actuation, and peak pressure within the dies (mainly for re-sizing) are not the same throughout the stroke, and this must simply be learned.
As perhaps we’ve made clear, choosing a system for fabricating your own ammunition isn’t as simple as, “These are good, and those are bad.” Even trading attributes among Iron Triangle criteria is of limited help. Next, we’ll take a look at why this is so, and importantly so. Much of it has to do with the calibers you’re thinking make sense to build, and especially if your goal is rifle, pistol or both.
Frank Winn has been studying arms and their relationship to tyranny, meaningful liberty and personal security all his adult life. He has been a firearms safety/shooting instructor for more than 20 years, and earned state, regional and national titles in several competitive disciplines.